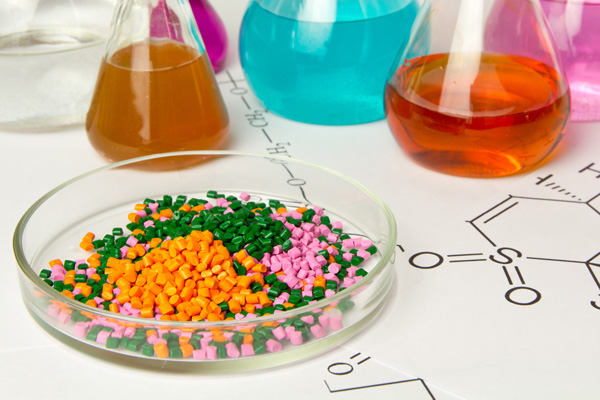
3 Essential Tips to Consider Before Starting a Plastic Molding Project
Plastic molding or injection molding is a manufacturing process employed for producing parts in mass production. It is used when the same part needs to be created thousands or even millions of times.
First, plastic molding involves the creation of a mold which is made up of two halves: a fixed and a moving part. The mold’s design must allow for easy injection of the elements, which are installed in an injection molding machine that firmly presses the two pieces together. Then, in the form of pellets, the material is poured into an endless screw which is heated. The screw transforms the pellets into a molten, formable plastic material which is stored at the front screw before the injection. The material is injected under high pressure and heat, ensuring the mold is filled before the material solidifies. Then, the content is finally cooled and removed from the mold, and the process is repeated.
There are significant benefits to injection molding. The main benefit is its ability to produce large product volumes. On top of that, the more products produced, the less the cost. Compared to traditional methods of manufacturing, injection molding produces low scrap rates. Although fairly straightforward, this process demands detailed planning if the finished product is to meet the required outcome. Here are three tips to consider before looking for plastic injection molders in California or elsewhere.
Design
Coming up with a clearly defined concept goes a long way in ensuring the production process is carried out efficiently. Establish the design goals and determine which have the highest priority. Is the objective to reduce manufacturing costs, simplifying the product’s design or to improve functionality? It’s recommended that you prepare details about your specific parts’ needs. Supplying this information to a plastic injection molding manufacturer will be valuable. Consider the size and complexity of the piece. Intricate designs need detailed molds. Lastly, look into the different types of materials, deciding the best one for your part. Many design factors will help with this. Try to understand the materials available and how they react to the different environments your piece will be exposed to.
Production
Volume consideration is an essential factor for injection molders. Injection molders mostly categorize their business as high or low volume. Low volume deals with production run below 10,000 parts. High volume might involve runs over 750,000 parts.
Additionally, there are a few types of injection molding technologies: traditional injection molding, structural foam injection molding, gas-assisted injection molding, and over-molding (combining two or more molded parts to make a single finished part).
Next, analyze the time it takes from initial concept to finished product. Discuss any time constraints from the beginning. The best scenario is one that allows enough time for any potential delays that might appear in either design revisions, manufacturing or shipping.
Costs
The initial investment of injection molding is significantly higher than the rest of the production costs. The investment typically includes designing the prototype and creating a mold to create replicas of the desired part. This process requires extensive testing, which ultimately takes up a lot of time and money.
After this is complete, it’s necessary to determine the number of parts that need to be produced for the injection molding to be cost-effective. Does the volume justify the cost? What is the cost-per-part that will guarantee the project’s profitability?
With these considerations in mind, the next step is choosing a plastic injection molding manufacturer. Read more about injection molding on our blog and find out why Valencia Plastics is the right fit for you. We’re happy to answer any injection molding questions you may have, and you can contact us for a quote today.
0 Comments
Leave a reply
You must be logged in to post a comment.